생산기술연구원 지창욱 박사, 금속 3D 프린터 개발
기존 주조공법보다 2배 빠르게 제품 제작 가능
2개월 걸리는 2m 선박 프로펠러 3주만에 제작
기존 주조공법보다 2배 빠르게 제품 제작 가능
2개월 걸리는 2m 선박 프로펠러 3주만에 제작
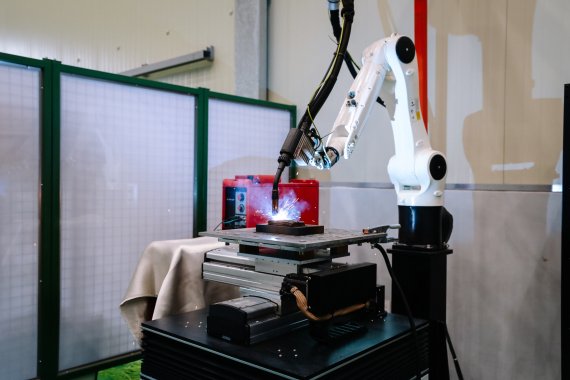
한국생산기술연구원은 첨단정형공정연구그룹 지창욱 박사팀이 금속 와이어를 빠르게 쌓는 '와이어 아크(Wire+Arc) 3D 적층 제조방식'을 고안해 금속 3D 프린터를 개발했다고 15일 밝혔다. 이번 기술개발을 통해 현재 관련 SCI급 논문 5편이 발행되고 특허 4건이 출원된 상태다.
연구진은 이 기술을 이용해 통상 2개월가량 소요되는 2m 크기의 대형 선박 프로펠러를 3주만에 만들었다. 또한 강도·내구성과 같은 물적 특성의 우수성도 인정받아 '선급 인증'까지 받았다.
지창욱 박사는 "이 기술은 자동화 용접시스템과 캐드 도면만 갖추면 중소 제조업체들도 쉽게 도입 가능한 고속·저가 3D프린팅 기술"이라고 설명했다.
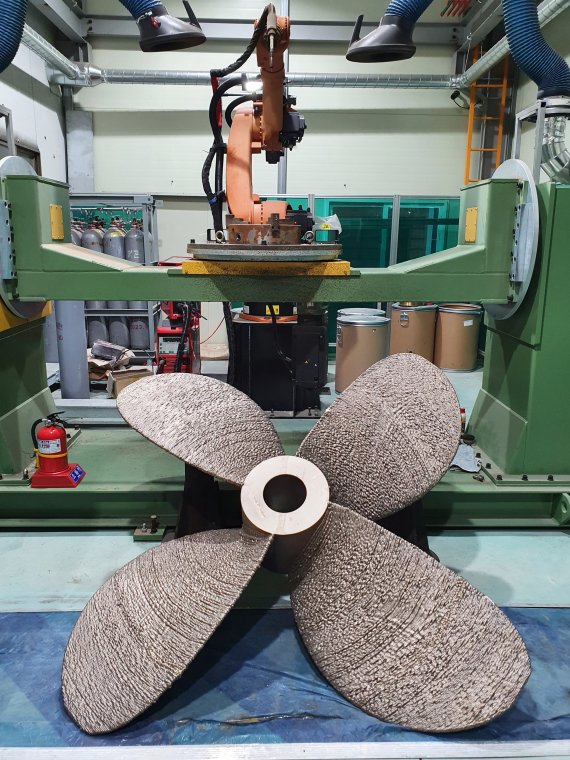
이 기술은 제작할 부품·제품의 캐드(CAD) 도면을 시스템에 입력하면 경로설정 소프트웨어가 최적 적층경로를 선정, 로봇팔에 부착된 용접토치가 그 경로를 따라 와이어를 녹이며 층층이 쌓는 자동화 방식이다.
이 방식은 부품 제작 속도가 기존 주조공법보다 2배 이상 빠르고, 특히 다이캐스팅 금형 제작의 경우 CNC 가공법과 비교해 제조단가는 약 20%, 소재 손실율도 80% 더 낮다. 장비 구축비용도 대형 3D프린터의 10분의 1 수준에 불과해 경제적이다.
또한 쌓는 과정에서 서로다른 소재를 접합하는 용접기법인 '클래딩' 방식도 적용할 수 있는데, 이를 통해 금형의 냉각속도, 내마모성 등을 향상시켜 금형 수명을 늘리고 제품의 치수 안정성까지 높일 수 있다.
지창욱 박사는 "향후 적용소재를 철, 알루미늄뿐만 아니라 경량화에 유리한 마그네슘 합금으로 확대하여 항공부품 제작에 활용할 계획"이라고 말했다.
한편, 각종 부품 대부분이 금속소재로 이뤄지는 제조업 특성상, 제조혁신을 이끌 핵심기술로 '금속 3D프린팅'이 각광받고 있다.
금속 3D프린터는 복잡한 형상의 어떠한 금형도 높은 정밀도로 맞춤제작이 가능해 시제품 개발부터 양산까지의 제품 라이프사이클 비용을 효과적으로 절감해준다.
특히 선박, 항공기 등 중대형 수송기기 부품처럼 부가가치가 높지만 다품종 소량생산이 필요한 경우, 가장 효율적인 대안으로 꼽힌다.
금속분말을 녹여 쌓는 'PBF' 방식의 기존 3D프린팅 기술은 고출력 레이저장비와 값비싼 분말 재료로 오랜 시간 한 층씩 쌓아야하기 때문에 금형이 커질수록 제조단가는 높아지고 생산성은 떨어진다.
또한 대형 금속 3D프린터 1대당 가격이 약 10억원 이상의 고가여서 중소기업들이 이를 도입해 운용하기에도 재정적으로 부담되는 상황이다.
monarch@fnnews.com 김만기 기자
※ 저작권자 ⓒ 파이낸셜뉴스, 무단전재-재배포 금지